Optimizing Locomotive Energy Management Systems (EMS)
August 19, 2020
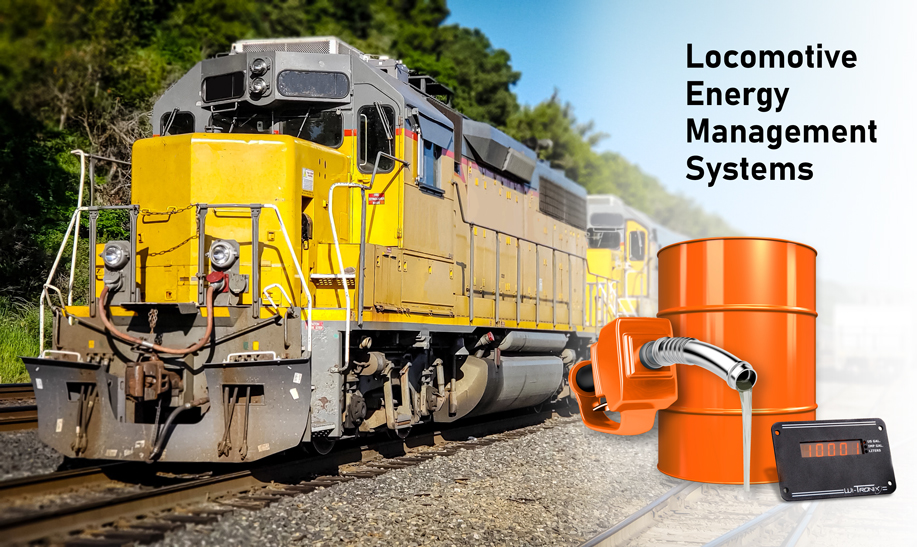
This is the third part in a series about fuel conservation. To read the first post in this series on The Need for Accurate Fuel Consumption Data, click here. To read the second post in this series on Locomotive Idle Reduction, click here.
INTRODUCTION TO LOCOMOTIVE ENERGY MANAGEMENT SYSTEMS
Energy management technology has been in development in various forms of implementation for almost fifteen years. First implementations were advisory in nature, however over time, the technology has matured into a fully automated cruise control system. This important aspect of Energy Management has great potential to save significant amounts of diesel fuel while protecting and even enhancing the fluidity of a customer rail network. Proper understanding of the why and how it saves fuel, along with tailoring the tool to fit within a given railroad’s operations, is paramount to optimizing the degree of fuel savings. A proper fuel consumption measurement tool and fuel savings methodology drives the entire process of leveraging and optimizing this important fuel efficiency technology.
Different vendors of EMS approach the task of energy management in different ways. While the algorithms may differ, the critical information to drive the system remains the same. A sample of key information that EMS requires and / or utilizes is listed below:
- Train length and weight
- Track conditions and grade / curve locations on any given route
- Speed restrictions and approaching signal conditions
- Spacing for adequate stopping distance for traffic ahead or appropriate signal conditions
- Number of cars and distribution of loaded and empty cars for proper train handling considerations
- Distributed power and where in the train additional locomotives are placed (mid train, through train and end of train)
- Type of locomotives within the train and their rated tractive horsepower
- Maintaining a trip schedule with arrival parameters within a specific time distribution window
- Monitor and minimize wheel slip conditions and measure rolling resistance / environmental effects
- Adequately discriminate track ID and location where there are double and triple track configurations
While EMS systems do provide fuel savings, it is a combination of the EMS system with EMS performance monitoring, accurate fuel measurements, and changes to dispatch and business practices that provide maximum fuel savings
ACCURATE FUEL MEASUREMENT IS A CRITICAL COMPONENT TO OPTIMIZE PERFORMANCE
The main tasks of energy management systems are to reduce fuel consumption and associated emissions, improve train handling, and integrate into the larger PTC package of tools. Having an accurate fuel measurement system is crucial to understanding how much fuel is being saved, and under what circumstances.
Using dummy figures for fuel savings, and measurement accuracy for illustration:
If a target EMS fuel savings is 5% and the measurement system accuracy of the fuel measurement system is in the 3% to 5% range, or depending on operating circumstances and locomotive on-board systems, then the ability to truly measure the EMS fuel savings component is virtually impossible, or at best severely compromised.
A signal to noise ratio is a measure used in science and engineering and has applicability to this discussion. The desired signal is the level of EMS fuel savings and the background noise is the accuracy of the fuel measurement system. The marketing literature for various EMS vendors has a wide range of promised potential savings, from low single digits of 3% to moderate double digits of 15% or more in some unique situations. If we consider a moderate average EMS savings of 6%, then the fuel measurement system needs to have an accuracy of somewhere between 2% to 3% to be able to properly discern the average 6% fuel savings. Otherwise, a wide range of fuel measurement error will result in a very wide range of potential EMS savings, likely from no savings at all (or negative savings) to something unrealistically and erroneously high. A possible but not recommended avenue around this conundrum (say the fuel measurement system error is in the 5% or higher range), is to track many thousands of individual trip segments to analyze, which is time consuming and cumbersome and rarely produces the desired result.
THE HOW AND WHY OF FUEL SAVINGS DELIVERED BY EMS, DRIVES PERFORMANCE
Understanding the conditions that lend towards fuel savings and those that do not helps to optimize the technology. For example, climbing a steep grade with a heavy train and all pulling locomotives at maximum throttle, there is virtually nothing that EMS can do in that situation to save fuel other than reduce the throttle and slow the train down, which in most instances is unacceptable. The only acceptable situation would possibly be if there is congestion ahead and the train schedule is already compromised, and maximum velocity is no longer necessary. Likewise, going down a steep grade and being in dynamic brake also provides little opportunity for EMS to save fuel. Though traveling through undulating or flat territory, which is most common, presents a great opportunity to save fuel. There are many variations of this simplistic example, including the degree of track curvature, train length / weight, train type, and traffic ahead (pacing consideration) to name just a few.
Leveraging the EMS fuel savings based on these types of operational considerations is critical to optimizing the amount of total fuel saved on a given railroad territory. Operational customer service considerations always take priority, but savings can still be optimized using this situational awareness approach.
LEVERAGING TRAIN SCHEDULE TO FUEL SAVINGS – AN IMPORTANT DYNAMIC
The largest fuel savings optimization arrow in the EMS technology quiver is the ability to modulate train schedule. Minimum time offset (MTO) is the EMS language of schedule sensitivity. A rail network is always changing real time, based on weather, congestion, and other episodic events, such as service disruptions. While all railroads strive to minimize the disruptions within their control, there are always those (like Mother Nature) which require last minute adjustments. Giving permission to EMS to take extra time to traverse a given trip segment based on factors ahead (such as congestion) is one of the largest opportunities to maximize fuel savings with EMS.
While these situations do not happen frequently, being able to take advantage of when they do will increase overall fuel savings from EMS technology. An example could be a congested yard ahead where it is a known fact that a train 2 hours from yard arrival will need to wait an additional hour to enter the yard. Giving that train the extra hour in transit time will increase the potential fuel savings for that portion of the trip significantly. These types of events can move a complete trip segment fuel savings from mid-single digits as a percentage to low double digit levels, not an inconsequential increase.
Having the systems in place to identify and take advantage of these types of situations in real time is not a trivial task. But the benefits of doing so will be more richly rewarded in terms of extra fuel savings from EMS technology.
DRIVING VENDOR IMPROVEMENTS
Any vendor worth hitching your wagon to, will be constantly striving to improve their product offering. Working collaboratively with your EMS vendor(s) will not only improve the functionality and reliability of the product offering, but also maximize the associated fuel and emissions reduction realized long term.
Being able to accurately measure fuel consumption and the associated fuel savings (or lack thereof) from the EMS product is where a healthy and much needed railroad / vendor relationship starts. Agreement on the measurement system accuracy and the methodology used to determine the fuel savings from EMS is absolutely critical. If the vendor uses a methodology that isn’t approved by the customer railroad, the stated vendor results will always be suspect. Likewise, if the vendor doesn’t agree with the methodology that the customer railroad is using, then their motivation to help improve the product based on fuel saving metrics will be compromised.
Operational considerations have to drive improvements. Train velocity and adherence to schedule are overriding concerns placed above the level of EMS fuel savings. Yet improvements can still be made to continue to optimize the level of fuel savings that EMS ultimately will deliver in the long term.
PUTTING YOUR ENERGY MANAGEMENT SYSTEM TO WORK – SAVING MORE FUEL
There are many different measures that can be gathered from the EMS on-board information and put into useful dashboards for continuous improvement. A list of potential target opportunities are:
- What percentage of a crew trip is EMS being utilized – how does this compare to the system goal?
- Can real-time alerts be created for Dispatchers to intervene when EMS isn’t being used by the Engineer operator, but should be?
- Identify the different reasons that EMS isn’t being used when it could or should be – segment the reasons and work on reducing each reason code as needed
- Create reports on EMS crew trip savings by location and train type then leverage the high savings locations – what is unique about the high savings trips that can be replicated across other system locations?
It is critical to considering how railroad business practices and monitoring of EMS performance can lead to enhanced performance of EMS systems.
Increasing the realized fuel savings from EMS is similar to doing a rolled throughput yield exercise, which is a quality tool. There are several “gates” which must be open to allow progression to the next step and only when all gates are open, can the actual fuel savings be gained. Some of these steps or gates are:
- EMS has to be installed on the lead locomotive
- EMS has to be working properly on the lead locomotive
- EMS has to be initialized before leaving the yard
- EMS has to be utilized by the Engineer operator
- The route grade and signals have to be programmed into the EMS system including appropriate slow orders
The EMS product can have a high single digit fuel savings potential as a percentage savings when everything is working properly, but due to the multiple gates required to pass through for success, if they are not all functioning at a high level of utilization, then the realized fuel savings for the system could be down into the low single digits as a percentage of fuel savings.
EACH RAILROAD IS A DIFFERENT ANIMAL WITH UNIQUE NEEDS AND PRIORITIES
There are seven Class I railroads and hundreds of smaller passenger and Class II and Class III railroads in North America. It is stating the obvious to say that each one is completely unique – from the topography to how they choose to operate trains over their network. The culture is deep and the histories long and storied – the same can be said for how each approaches fuel savings using EMS technology. One railroad may operate with a very low horsepower-per-trailing ton and thus operate in the highest throttle notch a high percentage of the time: EMS fuel savings potential for them will be reduced due to how they choose to operate their network. Another railroad may have significant grade on their territory and thus require a higher horsepower-per-trailing ton to accommodate: their EMS fuel savings potential will therefore be on the higher end of the scale.
Wherever a given railroad is on that spectrum of operational variability, there is always the opportunity to save fuel using EMS technology, and to optimize and increase the level of fuel savings that it will deliver over the life of the product. The desire and capability to chase ever increasing levels of fuel savings may be the only unique qualification remaining once all the other structural and operational differences between individual railroads have been removed.
CONCLUSION
EMS technology has a long history of development and improvement for both freight and passenger railroads. The potential to deliver both fuel and emissions reduction remain strong, and improvements will likely continue into the future for many years to come. The difference between moving forward elegantly or somewhat clumsily relies in large measure to the accuracy of the fuel measurement system, the methodology used to determine fuel savings, and how and why those fuel savings are achieved.
A potentially elegant EMS solution / approach deserves an equally elegant fuel measurement system and saving analytics methodology to work hand in glove towards driving significant improvement for future fuel and emissions reduction. EMS systems alone do not maximize the fuel savings value to railroads. Instead, it is a combination of EMS systems, EMS performance monitoring, accurate fuel measurements, and changes to dispatch and business practices that provide maximum fuel savings.
If you are interested in learning more, contact us by clicking here.
To read the first post in this series on The Need for Accurate Fuel Consumption Data, click here. To read the second post in this series on Locomotive Idle Reduction, click here.