Case Study: Locomotive Idle Reduction
July 8, 2020
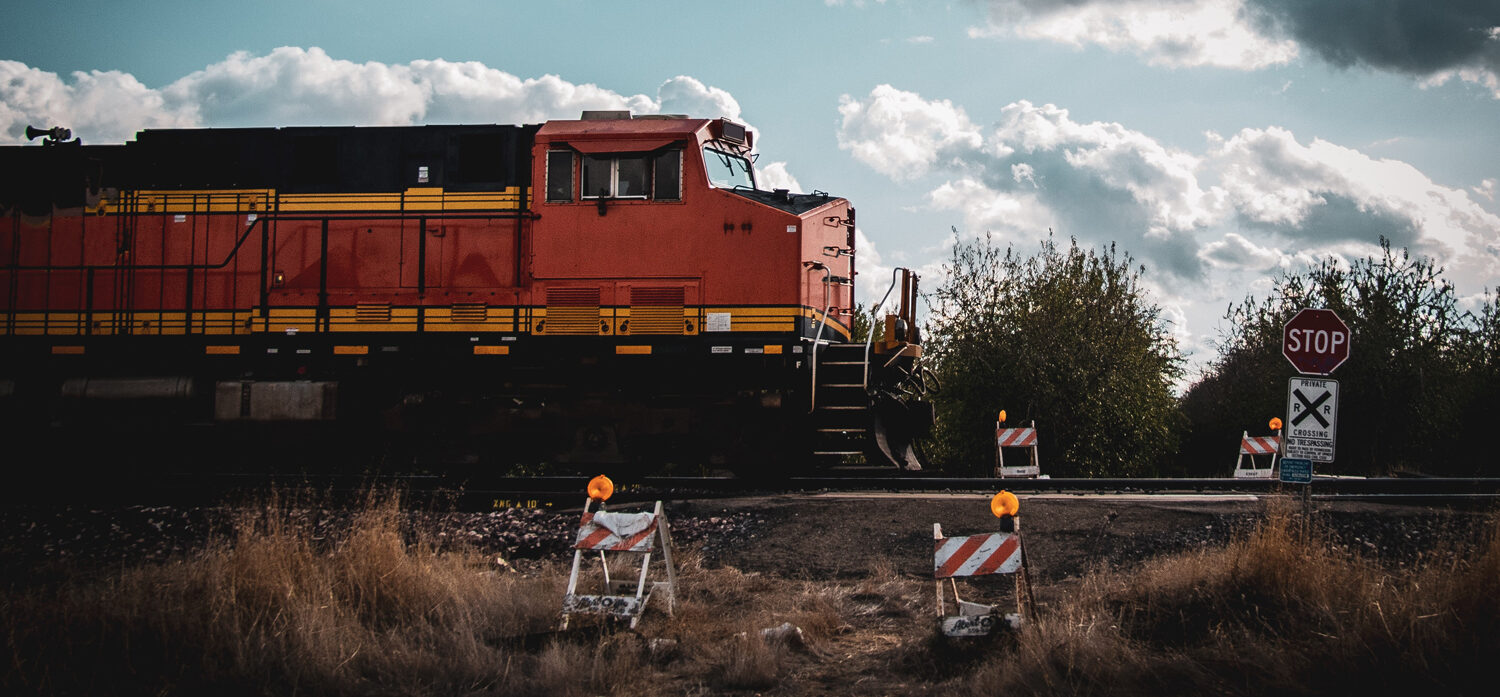
This is the second part in a series about fuel conservation. To read the first post in this series on The Need for Accurate Fuel Consumption Data, click here. To read the third post, Optimizing Locomotive Energy Management Systems (EMS), click here.
INTRODUCTION TO LOCOMOTIVE IDLE
Locomotives spend far too much of their service life with their diesel engines idling, which creates an issue for railroads in terms of needless excess fuel consumption and GHG emissions, as well as a “bad neighbor” badge from the general public who happen to live near railyards where a lot of excess idling with associated noise and emissions occur.
As to the why, the usual operational responses include, “It’s easier to keep it idling than to shut it down and have to restart it later, restarting a locomotive takes a lot of time” or “I can’t risk the chance that it won’t start again when I need it – what if the batteries are weak, or it has a bad starter?”
SO HOW MUCH EXCESS FUEL ARE WE TALKING ABOUT HERE?
Good question – is this a big deal or a little deal in terms of fuel savings? Let’s do a simple “thought experiment” – say I’m a railroad that consumes 500 million gallons of diesel fuel per year and I have 4,000 operational locomotives, both high horsepower line-of-road and lower horsepower yard units combined. Choosing a very conservative 4 hours per day that each of these locomotives are idling where they could have been shutdown and not negatively impacted operations. Using an average of 3.5 gallons of fuel burned per hour idling per locomotive – some easy math shows an annual consumption of over 20 million gallons of excess idle, which is over 4% of the total annual fuel consumption for that particular Class I railroad – do we have your attention yet? If the price of diesel fuel was $2.00 per gallon, this translates to $40 Million – and that is an annual savings not a one-time savings. That is a lot of fuel and a lot of potential budget impact.
TECHNOLOGY TO THE RESCUE? – MAYBE, MAYBE NOT
There are certainly technologies available and in use that help to address the excess idle issue. AESS Systems, or Auto-Engine-Stop-Start Systems, have been in use for a few decades. Auxiliary Power Units (APUs) have seen various levels of use for years as well. APUs typically use a very small installed diesel engine to do all the functions the larger prime mover engine would do otherwise (water heated, battery charged, air systems primed, power to sub-systems) at a fraction of the diesel consumption, usually between one quarter and one half gallon per hour. APUs just don’t provide power to move the locomotive.
Why do these technologies sometimes not live up to their potential? Let’s start with AESS; there’s a limit to how many times a large diesel engine can be shutdown and started in any given 24 hour period – otherwise you begin to prematurely wear out your engine starting system components like starters, batteries and contactors. Road failures caused by starting system problems greatly magnify the cost impact on the railroads – it isn’t just about maintenance and component costs. There is also the human factor to contend with – any of these systems can be manually disabled by human intervention for a variety of reasons which may make sense at the time but combined together can really reduce the efficiency of the system and reduce fuel savings. System reliability carves some savings away as well – maintaining systems, like APUS, that are not “mission critical” can sometimes leave these devices with lower availability statistics than is desired. Cold weather operations are another problem for AESS operations, as locomotives have water cooled engine systems which can easily freeze during cold winter operations where AESS is much less effective. This was one of the reasons for the introduction of APU technology. However, a common complaint for these systems include having another diesel engine to maintain with regular tune-ups, engine oil changes, belts, reliability issues, etc… There is no doubt that technology can prove helpful in reducing engine idling, but more is needed to maximize the fuel that can be saved.
A CONCERTED EFFORT IS REQUIRED
There are many professionals who maintain, operate, move, and inspect locomotive diesel power. They can – and should – each play an important role in minimizing excess locomotive idling. We’ll go through each craft within the Transportation and Mechanical departments and speak to how they can assist with reducing excess locomotive idling.
- Locomotive Engineer – Once they take control of their train and check their paperwork, they can confirm which units should be pulling the train and, weather permitting, which locomotives should be shutdown.
- Locomotive Yard Hostler – Depending upon what time any given locomotive in a yard is scheduled to move onto a train or into the shop for maintenance, they should be shutdown if the time is more than a set parameter, usually something in the 30 to 60 minute range.
- Locomotive Maintainers – A locomotive shop is usually very busy depending on the amount of traffic any given day. Locomotives typically will wait outside a maintenance shop, waiting for an open bay to perform required maintenance. A similar tight window should be used where, if the locomotive is not expected to be moved for 30-60 minutes, it should be shutdown. Note that even low temperatures in the dead of winter need not interfere with shutting down locomotives for a few hours, given there is enough latent heat energy remaining in the locomotive engine water that it will be several hours before the risk of the locomotive dumping water due to below freezing temperatures. Local rules for that shop, depending on their geographic location, should determine the specific rules for that area of the network.
- Management personnel, such as fuel analysts, work with the IT department to create and maintain a reporting dashboard or scorecard to track fuel savings. Management needs to drive and orchestrate the process, marshal the separate departments and craft professionals and set appropriate goals for the future.
The key to a concerted effort is everyone working together to ensure idle time is reduced. A good way to check this is to walk through a locomotive yard and count the number of locomotives idling. Some observations over the period of an hour or two, noting time and locomotive road number, can yield some excellent visual observation audits as to how well the shutdown rules are being followed.
A REAL-TIME MEASUREMENT SYSTEM
With on-board technology on most modern high horsepower locomotives, the GPS location and idling status can be reported in real time for a majority of the locomotive fleet. Using predetermined geofenced limits for any given yard, a scorecard can be developed that measures compliance to the local shutdown rules – how long was a given locomotive idling without moving. This scorecard, when shared with management and the employee workforce, can build business processes and direct effort towards decreasing excess locomotive idling within the yard limits where most idling occurs.
Further, these systems can send out alerts to operating management by text or email with appropriate escalating time triggers to drive and support the needed behaviors to reach a higher level of compliance. Whatever grade or percentage compliance a certain location achieves can be improved upon, and yearly goals for improvement set and achieved with all the personnel working together to achieve the set system or location goal. The performance management teams at different shops can also be directly compared and local best-practices leveraged across the network.
Figure 1 below shows an example of a scorecard which tracks both excess idle in minutes and the associated fuel expense by location, as well as the number of excess idle events grouped into discrete time measures.
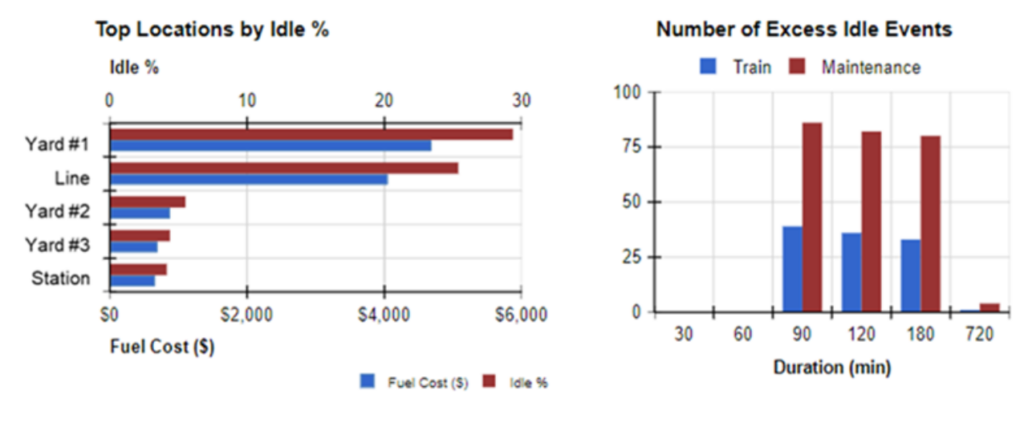
Figure 1
Figure 2 below shows both historical temperature by month and the number of excess idle hours year over year. Goals for both Figures have not been shown as each railroad will have varying goals and timelines for improvement.
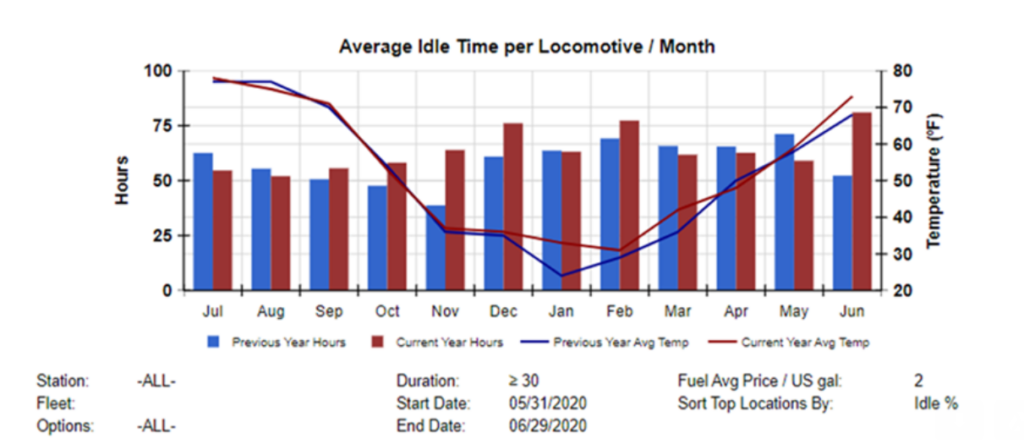
Figure 2
SIGNIFICANT REDUCTIONS ARE POSSIBLE
With the support of local shop management and setting appropriate improvement goals, long term significant change is possible when all employees do their part to insert themselves into the reduced idling equation. With proper training, tracking, and reporting, idling reduction of 50% or more is certainly achievable. Proper maintenance and servicing of the available AESS and APU technology should also be part of the overall plan for improvement. Human involvement is always preferred to a “the technology will take care of it” approach.
CONCLUSION
Human and machine working in concert, with an approved training plan and a real-time reporting scorecard with drill down alerts and performance metrics, will absolutely have the desired effect of driving down excess locomotive idling. Properly maintained technology – where available – can be an excellent servant in helping achieve realistic and aggressive long term goals. All yard personnel, including the locomotive crew, play a specific role in making sure they are individually responsible for their area of performance. Thinking that someone else will take care of it will only lead to frustration and disappointing results. A 2% to 3% or more fuel efficiency improvement is attainable depending upon the baseline level of performance already in place. This provides the benefits of year-over-year fuel savings, cost savings, and the added benefits of exhaust and noise emissions reductions.