Why Embracing Data is the First Step to Digital Transformation in Rail
March 11, 2019
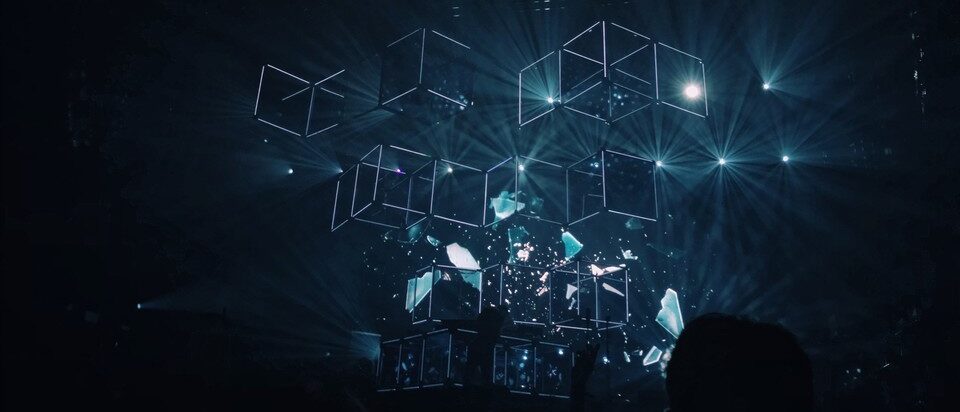
Last month’s rail carload volume increased by 3.2 percent and intermodal volume was the second highest for any month in history at 6.6 percent. A strong economy and demand have driven some of that growth, but some wonder how much better it could have been if rail service levels met industry expectations.
It’s a great question to ask as the rail industry experiences a pivotal moment to embrace digital transformation technology. Many executives are faced with the urgent decision to exchange outdated business processes for more holistic systems-based approaches or continue on their conservative paths. Those who choose the latter will miss the opportunity to drive efficiencies, reduce waste, and lead the industry.
What does it mean to embrace digital transformation in the rail industry? It means integrating complete, end-to-end solutions that combine, normalize and showcase data in a way that enables rail companies to use it to drive short and long-term business decisions. Locomotives are essentially mobile data centers. Why aren’t we treating them as such? Uniting disparate data is critical to making informed decisions on everything from locomotive usage, mechanical maintenance, risk and compliance, capital planning, safety and more.
Many rail companies say they are actively capturing and using data, but the majority of them are doing so in small buckets and, more concerningly, in silos. They’re not integrating it within their systems and not effectively changing processes that allow them to successfully leverage the digital transformation that is occurring. A complete platform, if implemented correctly, will create real value for rail companies. For example, if you had an event that required you to pull your event recorder data five to 10 years ago, how did you do it? Similarly, how did you monitor the health of the lead locomotive event recorder? It is probably not very different from how you do these activities today. In fact, more than 21 percent of monitored assets in service have a failed event recorder. All of this is to say, most companies are implementing IoT but failing to change the outdated processes that are required to realize the true value.
At Wi-Tronix, we’ve seen the impact of embracing future-looking business processes and the power of integrating solutions. Our customers that have used a connected approach to their businesses have seen the results for things like fuel monitoring and waste reduction, event recorder technology, digital video recording systems, control systems, and overall user experiences.
At the core of connectivity and the internet of things (IoT) is a data set that can be used. One of the biggest challenges to the rail industry is data fragmentation. Each locomotive has its own data, in its own structure, with its own naming convention, with each slice of data viewed in disparate snapshots. The user experience is very clunky, disjointed, and makes it difficult to take action on the information. For example, looking at something as simple as “locomotive identification” would be challenging because GE, EMD, and MPI all have different naming conventions for it.
In your personal life, how likely are you to keep technology or a device that is difficult to use? You don’t. You either stop using it entirely or switch to a more simple option. This is why user experience is so important. At Wi-Tronix, we’re able to lay the foundation for data use and insights by providing a platform that self organizes the information and commonizes it regardless of where it came from. It draws a simple line from A to B so the user doesn’t have to learn multiple ways to read the same signal for different types of locomotives. We then provide a best-in-class user interface that brings all of the data together in one “dashboard” so that the rail decision-maker can spend their time making informed decisions instead of translating data architecture. No interpretation needed.
We also offer auto-self ACC discovery, which means a rail company can take our event recording device, or Violet or Wi-PU and it can go on any locomotive and the device self-configures to that particular type of locomotive. This better user experience is necessary because there are endless data points that can be monitored and used to decrease waste and increase efficiency. For instance, a few areas that we streamline and provide insights to our customer for are:
- Safety – This could include operator behavior monitoring, threshold-based alerts for things like overspeeding, and tracking for hard coupling, overshot station, power braking, throttle modulation.
- IT – We’ll handle configuration management and over the air updates.
- Claims and Risk Management – We provide support for chain of custody, evidence preservation, remote access to download the video recording system.
- Mechanical – We provide support on locomotive readiness and health reviews including things like faults that are actively occurring on the asset or ensuring that your lead locomotive ER, ACC and DVR working.
- Engineering Track – We’re able to help the infrastructure team identify rough track, rough riding areas, bridge approaches, collapsed culverts using our Wi-Nav detection.
The innovative ways we’re remote transmitting critical locomotive data off are actually very similar to the streaming methods of Netflix. For example, a truck was transporting fuel illegally and pulled in front train causing an explosive, fuel ball that consumed the locomotive resulting in a total loss in the data recorder’s crash hardened memory. However, with Violet we were able to alert the railroad to this event in real-time and offload all the data before the locomotive was completely consumed in the fire. This informed the dispatch of the exact location and confirmed all three crew members made it out safely. From the time of the event until the cab was consumed was 240 seconds. From time of impact to crew clear and off the locomotive 90… This means we didn’t lose any of the critical data leading up the event, during the event and when the locomotive came to a stop. Do your ER/DVR have the capability to offload critical video and event recorder data in real-time? This is critical to protect your railroad in high profile cases and to learn from these accidents.
For us, it doesn’t stop there. We’ve always focused on providing great customer service and experiences and offering simple user interfaces. Now, our recent investment from Siemens has enabled us to double down and take a large step forward to continue to focus on providing our customers industry-leading user experiences. We’ve hired more project managers from within the rail sector and beefed up our team of design experts who are modernizing the portal to further enhance the user experience with a large focus on mobile.
We’re also focused on the technologies that are coming down the pike, leveraging consumer technology to bring the next source of innovation in the rail space. While they may not be popular in all circles of the rail industry, like Tesla and Amazon saw from the consumer perspective, we believe that AI and deep learning are relevant to rail and are on an upward trend. We’re bringing the technology used on public highways to rail. For instance, voice computing, asset detection and AI for self-driving cars in a locomotive. The next major technology to drive change in rail might by connectivity that leverages communications delivery and real-time streaming that is similar to Netflix or Youtube.
These are all potentially future game changers for rail. Today, executives can start by embracing the digital transformation by using comprehensive data to inform their decisions, monitor their locomotives, increase efficiencies, and reduce waste. We take care of the heavy lifting with regard to our customers’ data integrations, so they can focus on up leveling their business processes to take advantage of the strong economy and drive even more growth.