The Evolution of Rail and Technology
August 23, 2019
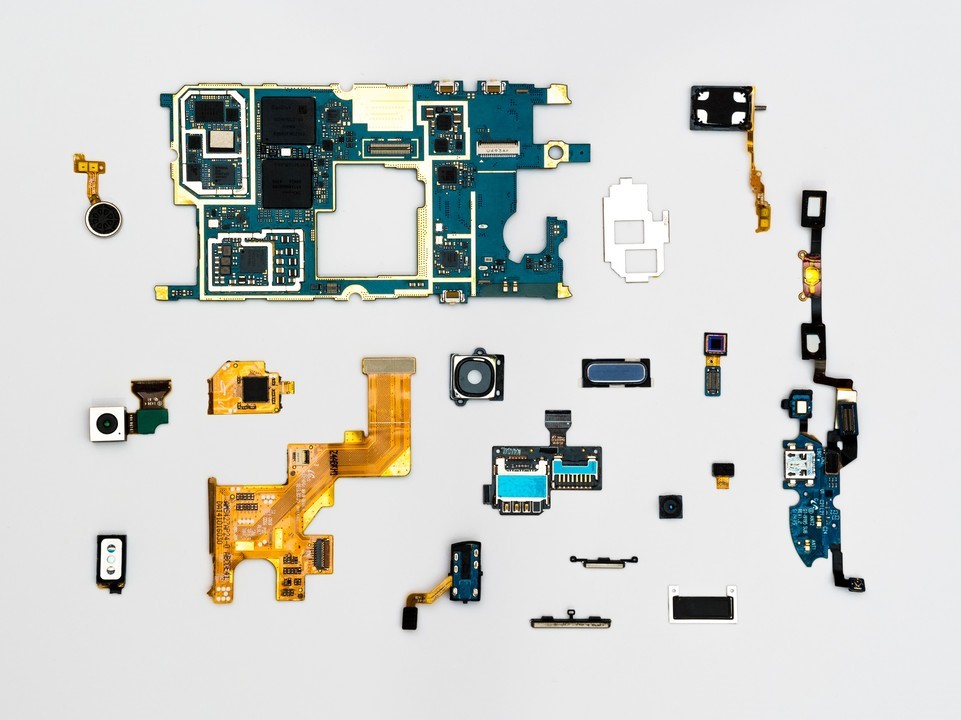
I’ve been in the rail industry my entire career. As an operator, there is nothing like the excitement and energy that you get while you’re on a locomotive in throttle notch 8. It’s always fun to see people wave to you when you’ve got a big train behind you. It’s just something that you can’t describe.
I love the way that the railroad industry connects everything – families to each other as well as consumers to the goods they need. The mission of the rail industry is super exciting — it’s to provide safe, reliable, and efficient transportation that meets customers’ expectations. So far in my journey in this industry, I’ve seen tremendous growth in leaps and bounds by deploying new technologies in safety, efficiencies, and driving customer outcomes. There hasn’t been a more exciting time in rail since its inception.
Early in my rail career, everything was focused on clipboards, paper, switch lists, printed documents, and all kinds of things that had massive inefficiencies. It was standard procedure to pick up the phone, and not just your cell phone or mobile device, to call dispatchers and give train orders. Today, most things can be automated. However, there are still several problems that can be solved by moving from analog to digital to drive better outcomes for all of our customers.
Throughout my career, I’ve had the benefit of seeing the industry from all sides. I started my career in the railroad industry at the ground level, then rose through the ranks to general manager, and finally made my transition to Wi-Tronix, which provides technology to railroad companies.
Over the course of my experience, I’ve seen three main problems: excess idle, fuel theft, and slow adoption of remote connectivity that enhances visibility to make real-time decisions. Previously, in the analog age, we solved those problems by throwing a massive amount of resources and human capital at it such as sending managers to physically drive to locomotives to collect particular data. This created massive amounts of inefficiencies and waste by not focusing on the true outcomes that we’re looking to drive: safety, reliability, and meeting customers’ expectations.
With that perspective in mind, knowing how far we’ve come from pen and paper to real-time remote connectivity, I sat down with a few folks from my product team and within the industry to hear their thoughts on digital transformation.
Mike Carter II, Senior Road Foreman of Engines, Indiana Harbor Belt (IHB) Railroad
I asked Mike Carter II, Senior Road Foreman of Engines, Indiana Harbor Belt Railroad to share some of the old processes and procedures that were in place early in his career as well as some of the pain points they caused.
MC II: Back in 2010 when I came on board, we used to have to chase down downloads for information in the case of an accident or if we needed to look into usage. Now it’s to a point where the event recorder is web-based and all the information we need is right there. I can see what’s going on right now, in real-time without having to download the data from the locomotive.
CJ: If you were to share your experience with someone that was thinking about digitizing their railroad and taking that step to leverage remote connectivity, what advice would you have for them?
MC II: One question I always get revolves around the inward-facing camera. How crews react to having an inward-facing camera in the locomotive. People thought that was going to be a hiccup in the beginning, but the more installs that we get, the more adapted our crews are. They continue to go on about their business just like the camera wasn’t there. It’s been a useful tool for both sides.
Michael Cunningham, General Director of Locomotive, Indiana Harbor Belt Railroad
Then I spoke with Michael Cunningham to hear his perspective on the types of digital transformation IHB has embraced and why they’ve taken those steps.
MC: Well some of the issues that we’ve had revolve around seeing the utilization of our fleet. A locomotive would leave the roundhouse and just go off somewhere. We didn’t know where it was going or what it was being used for. So digital transformation helps us keep track of how and where they’re being used. It’s also helped us track our fuel usage and the overall utilization of our fleet.
CJ: I’m super excited to be here on this CNG (Compressed Natural Gas) locomotive today. I mean it’s one of a kind. There aren’t a lot of companies that have taken the leap. How do you monitor your CNG now with this type of locomotive? This is leading-edge, breakthrough technology.
MC: Right, it is the first of its kind. We have onboard computer systems on the locomotive that monitor the usage, the temperature, pressure and more. Then at the fueling station where they compress the natural gas and send it over to the fueling station, they calculate fuel usage. This type of monitoring enables us to gauge how much we’re using annually or monthly and see what fuel savings we have.
CJ: What best practices, recommendations or processes have you been able to change using some of this type of technology?
MC: The number of locomotives that we have in our fleet and where they go has changed dramatically through digitization. So we’re able to see which yards use which locomotives and how often, and we’re able to build our plans from that.
CJ: Technology sometimes scares people and makes them feel uncomfortable. What were some of the hesitations and some of the things that you’ve been able to do to influence the adoption of technology?
MC: The railroad industry itself is an old industry and the guys are really set in their ways. So whenever they need to adapt and change, they can be really hesitant. So that’s where you go into the training of it and let them know exactly what it is and how they can use the technology to better their jobs and make them more efficient.
Then I sat in the hot seat. Mihir Phadke, Product Manager at Wi-Tronix, interviewed me on my take for the future of rail technology.
MP: You worked as an engineer and then worked your way up to become a general manager. In your experience, what are the different problems you’ve seen in rail and how do you see technology solving them?
CJ: We’ve talked about excess idle a lot and how we can empower good and informed decisions. Another is fuel theft and how we can alert in real-time and look at the whole supply chain of fuel from the time it’s delivered to the locomotive to the time spent. Lastly, remote connectivity and how it can bring new insights and visibility. Technology in these particular segments can really drive new outcomes and excellence in operations. A lot of people say real-time but they really mean that the information comes across hourly.
MP: As a product manager I see people say real-time and they actually mean once a day. In our case at Wi-Tronix, we are talking second by second data. We have the capability to stream event recorder video data truly in real-time. But the beauty of it is that we take all that data, we condense it, we digest it and we only give our customers an insight that they can take action on it rather than having to go through terabytes of data and spend lots of time building their own insights.
CJ: Exactly. Really the key benefit to having remote connectivity is so customers can actually act on that information immediately versus waiting until the end of the year to review annual reports to see how much fuel was used, how many locomotive miles were traveled versus how much fuel is burned, etc.
MP: From a product perspective, Wi-Tronix now has Violet, where it lets you download event data and video data offboard. What problems do you see Violet solving for customers and can you give us a couple of examples?
CJ: Back in the early 2000s, there weren’t digital gauges. We used sight glasses and it involved old analog gauges, which was very difficult. You’d have to get with the fuel team, find out actually how much fuel was put on board, and so on. Connectivity has allowed for speed of information. I can actually deal with my crew on the ground providing job safety briefings with them as they’re coming on duty; making sure they’ve got the right paperwork; making sure that they are set for their mission as they depart to go from LA to Barstow. And that’s their mission. Most of them are going those big long haul and we’ve got to make sure they’re set up for success.
After speaking with these industry experts and discussing where rail has been and where we believe technology is taking it, it became clear that it’s not enough to have the technology. You have to integrate the technology. And that requires all of us working together in a partnership so that we can all see successful outcomes tomorrow. Are you ready for that challenge?
Published on July 10, 2019 – by Chad Jasmin