Can Railroads Meet the 40% Increase in Demand by 2040?
August 1, 2018
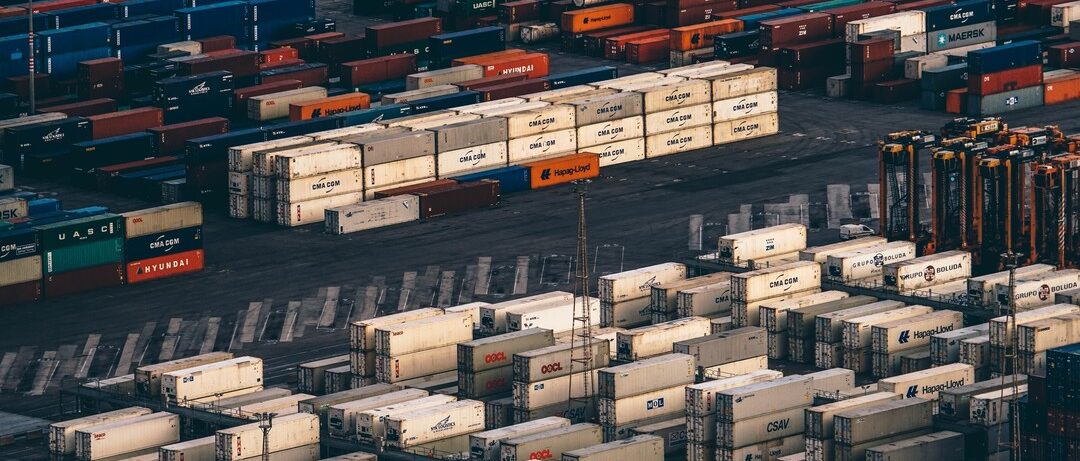
Hauling everything from coal to produce, railroads generate $10 of economic activity for every $1 spent. From 2015 to 2040, U.S. freight demand is projected to increase 40 percent. This presents an obvious opportunity, but railroads will have to compete with disruptors in the market who are promising customers the highest-velocity, lowest-cost supply chain. Railroads have to maximize efficiency today, so that they can maintain leadership into the future.
I mentioned in my last article, that disruption in transportation is happening across industries: automotive, rail, trucking, and even space. When Elon Musk announced the Tesla electric semi-truck, he threatened to disrupt freight railroads, claiming that by using platooning, they will beat rail with a more efficient alternative. Based on my math, the electric semi doesn’t beat rail in efficiency today, but the technology is designed to adapt and improve rapidly. The rail industry has to consider Tesla and other players in autonomous trucking to be genuine threats, and take action wherever possible to maintain an efficiency edge.
There are six components of rail operations that are low-hanging fruit for optimization: asset utilization, network optimization, fuel costs, infrastructure inspections, safety systems, and predictive maintenance. I’ll dive into the first three here, and address the final three in my next article.
Asset Utilization
We recently commissioned a study, which included a review of locomotive utilization. The results revealed that there is considerable opportunity for improvement. The image below outlines typical performance of locomotives in a Class 1 fleet. Locomotive utilization averages only 30%, and we’ve seen utilization rates as low as 17%.
While there is a lot of focus in the industry on optimizing maintenance, 50% of the time spent out of service by locomotives is managed through network planning, transportation operations, and engineering.
This is where continuous access to comprehensive data about the location, health, fuel levels, actual usage, and other key factors that affect utilization of locomotive fleets becomes critical. Having that data available exactly when and where it’s needed is the key to fully optimizing asset utilization. Connected, IoT-based solutions make it possible for rail operators to gain insight through analysis and to make real-time adjustments in the field when operations don’t go as planned.
At Wi-Tronix, it’s not uncommon for our railroad customers to reduce the number of locomotives on hand by 10 percent within the first few months because they have visibility into exactly which locomotives are being used and how frequently.
Network Optimization
Similar to monitoring and optimizing locomotive utilization, network utilization must also be optimized. Using data and analytics, network use can effectively run like clockwork ― which is required in order for freight and passenger traffic to flow seamlessly.
Unlike the flexibility trucking has using four lane highways with several exits and route options, railroad networks are like a series of single-lane, one-way roads that have to be scheduled meticulously. If you put too many trains on the network, there is too much traffic, causing congestion and risk of incidents. In order to enable more frequent, denser traffic, rail networks have to be planned and coordinated with a high level of accuracy.
The only way to accomplish this is with real-time visibility to every train in the network. Particularly, in higher speed areas where commuter trains can go 80 mph, but freight trains average just 30 mph, coordination is key so that freight trains don’t have to pull off and come to a complete stop to allow the commuter train to pass. This network coordination alone is an extremely important process that offers opportunity to maximize efficiency.
We solved this at Wi-Tronix, by giving customers the ability to not only use analytics to develop optimized plans, but also to understand what is happening in real-time so they can make adjustments to the network plan. From immediate updates regarding congestion issues, heat maps that show delay areas, and dashboards showing average velocity of a corridor, customers are able to optimize network use as efficiently as if they were directing traffic in person.
Fuel Utilization and Costs
Freight railroads are very efficient, hauling one ton an average of 479 miles per gallon of fuel, but volatile fuel prices and competitive pressures from disruptors who are closing the gap, make fuel costs an important focus for efficiency.
As you create efficiencies in how your assets are operated and your network is scheduled, your locomotives also operate more smoothly. Fewer traffic stops means less time wasted and less fuel needed to get back up to cruising speeds.
To fully optimize fuel costs, operators must have access very precise, up-to-the-minute fuel levels and the ability to combine that information with key trip data such as load, terrain, and weather conditions. By predicting how much fuel is needed between destinations, operators can manage speed and train handling based on load, terrain, and weather conditions so they use less fuel.
Operator control also affects fuel costs. Onboard, automated operator-assist solutions, such as our EcoRun product, are rapidly coming online to help operators with optimal handling. Using edge processing to adjust based on current conditions, with audio/visual cues to prompt in real time, these systems help operators maintain situational awareness and up-to-the minute knowledge of optimal speed and handling for greatest fuel efficiency. In the near future, we will see railroads begin to adopt more automation in this area, just as we’ve seen in the airline industry and are seeing in trucking.
With analysis and precise prediction of fuel utilization, operators can also plan their missions to refuel in areas where it’s cheapest, and decrease the number of unnecessary refueling stops. Redundant fueling stations that are either too close to others, or no longer a major stopping point, can also be closed down if networks are optimized, further decreasing capital costs for owners.
A comprehensive approach to managing fuel costs requires reconciliation of fuel invoices against actual consumption and fueling. The key here is accuracy and precision of fuel data and making that data available to accounting systems.
Managing fuel theft is also an imperative for many railroads in remote areas. This can be more challenging, but our customers in remote areas of Mexico and Australia are utilizing drones and locomotive video cameras combined with video analytics and real-time alerting to virtually eliminate the problem.
We routinely see customers reduce annual fuel spend by 10 – 15% when they adopt our IoT-based fuel solutions. For a Class 1 railroad, this can mean hundreds of millions of dollars in savings and goes a long way toward the levels of efficiency needed to help maintain leadership in the face of disruption.
Pallets of Cash
As you can see, railroads have numerous opportunities to use their data and IoT-based technologies to gain significant savings and create efficiencies. The question is, will they do it?
I often refer to Elon Musk’s approach to motivating his team to figure out a way to recover the $6 million fairings from SpaceX rockets by asking them to imagine the fairings as “pallets of cash” re-entering the atmosphere. When I look at the data and places we’ve been able to help our customers gain significant efficiencies there are clear “pallets of cash” waiting to be recovered for rail companies: asset utilization, network optimization, fuel costs, infrastructure inspections, safety systems, and predictive maintenance.
In my next article, I’ll dive into ways to use advanced technologies to optimize infrastructure inspections, safety systems, and predictive maintenance for greater efficiency.
Freight demand is set to grow 40 percent and trucking players utilizing autonomous electric truck platooning are prepared to come in and take significant market share from rail by selling customers on a more efficient freight solution. Efficiency is not an option.
Originally published on LinkedIn