Digital Video Recording: The Silent Witness
March 11, 2019
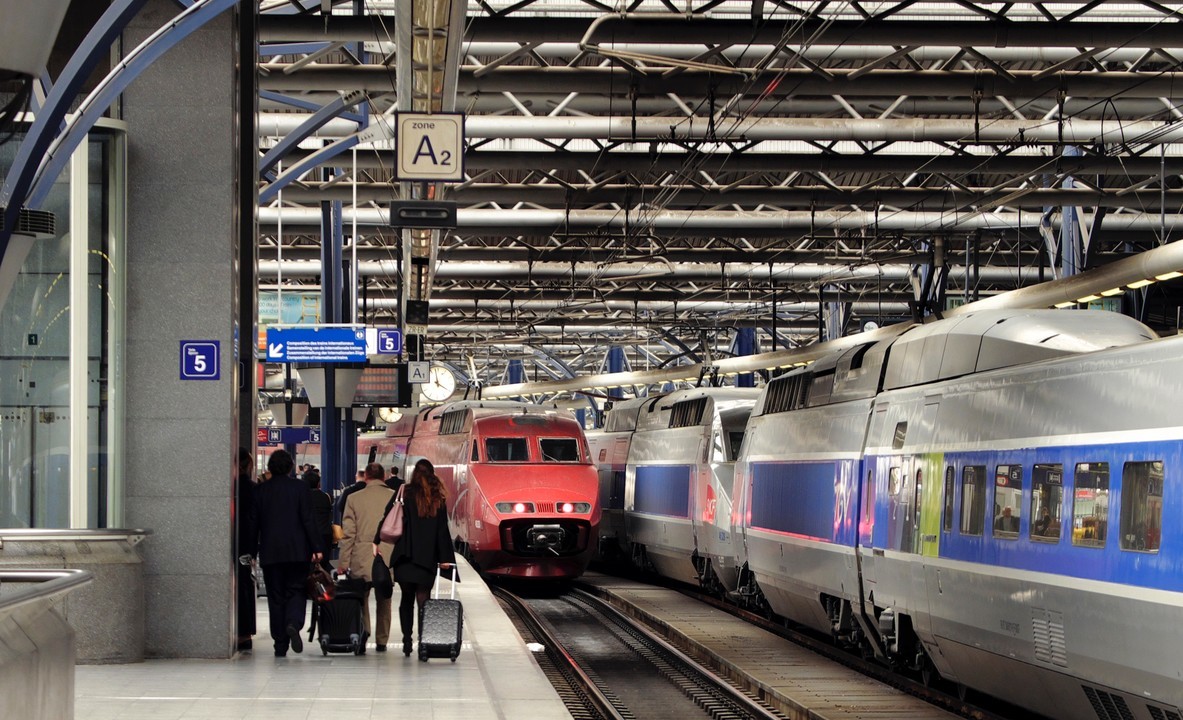
Rail operators take on a lot of responsibility. They have to get goods from location to location, on time, regardless of route issues. They have to take care of a $2.5 million locomotive and the hundreds of millions of dollars worth of train that trails behind it. They also have to keep public safety in mind as they pass through local towns.
When people hear of the devastation that occurs during a rail-civilian accident, often the first questions are whether or not the crew was at fault. Was the train operating properly? Were there track crossing signage issues? We all want to know exactly what went wrong.
At Wi-Tronix, this is one of the key reasons we believe rail companies should use Digital Video Recording (DVR) technology. We believe it is the silent witness that allows everyone involved in the investigation to focus on the most important part of an incident: the people.
In the majority of rail accidents, the crew has done everything right. In sensitive cases where they might have an incident at a crossing, DVR provides the unique ability for rail operators, attorneys, and those affected by the accident to see the full story play out exactly as it happened.
Having been on the other end of investigating these types of accidents, I know how traumatic it is for everyone, especially the crew. With DVR, the crew doesn’t have to answer tough technical and operational questions when they’re in a state of distress. Instead, the investigators can be human and ask them: how are you feeling? How can we help you? Can we get you a counselor? Do you need someone to take you home? Do you need time off? DVR allows you to stop all the mechanical questions and focus on the mental health of the crew.
Know the Facts
DVR allows you to see all the facts, know all the inputs, visualize them and experience them as if you were on board with the crew. Unlike the complexities of event recorder data, where you have to be an expert to know how to read it and understand it, and juries can interpret the findings differently, digital video recording is objective. It takes away doubt.
Reduce Cost and Stress
Having video reduces the cost and stress of most investigation cases. Even in the fraction of cases when the crew has made a mistake, video reduces the negative outcomes that the individual and the rail company face because there is no question of what exactly occurred. For rail companies that don’t have video on the lead locomotive, they automatically face increased scrutiny. If they did have video onboard, but there happened to be a failure with the DVR technology, the company faces additional examination of all maintenance practices and other areas of operations. Then, every aspect of your train and operations are reviewed: education, training, other data logs, and more. Plus, the cost of the case goes up if a critical system is offline or failed at the time of the incident.
IoT and Connectivity Reduce Risk
This begs the question: why wouldn’t rail CEOs and CFOs use the Internet of Things (IoT) to ensure their locomotives and all of the components onboard like event recorders and digital video recorders are working properly 24/7? Many DVR systems being purchased today do not have remote connectivity for health performance monitoring and don’t alert you when there are exceptions. Without automatic health monitoring like Violet or Wi-PU, systems are often only inspected every 92 – 184 days. That’s a window of three to six months where you run the risk of having an onboard system that could be down when you need it most. From our perspective, that’s an outdated practice.
Wi-Tronix not only has our own video recording system, but we can also integrate with other third-party systems which allow us to remotely monitor the performance of all systems on the locomotive in real-time. Our technology can report back when a lead locomotive’s video recorder or other system is not working, enabling railroads to take informed action immediately to resolve that conflict. Whether that involves swapping that locomotive out or replacing the DVR, it reduces the risk to the railroad while also protecting the crew that’s onboard.
Embracing real-time connectivity requires a shift in mindset. Valuing hourly performance monitoring is a new way of thinking about asset health. For those rail companies that embed Wi-Tronix into their entire operational approach, they’re changing their process and outcomes for the long-term by leveraging an IoT protocol. It tracks ER and DVR function, as well as everyday operational controls like fuel savings, train handling, emissions reductions, track geometry and mechanical wear.
Performance monitoring technology is essentially an insurance policy that can save you scrutiny, stress, cost, and liability if an incident does occur. Rail operators and crews are responsible for taking care of multi-million dollar machinery, goods, and the safety of those around them. Why not invest in technology that provides peace of mind today, and everyday? Whether you use Wi-Tronix or another system, we implore you to leverage technology that will protect your crew. I look forward to hearing your perspective and thoughts on the topic.